Service: Concrete repair works
Location: Teesport
Client
PD Ports operate major port and logistics sites on the east coast of England. Teesport is PD Port’s sixth largest and busiest port in the UK, handing 28 million tonnes of international imports and exports per year.
The problem
In March 2024, PD Ports called upon OnSite Specialist Maintenance to carry out concrete repair works to twelve shipping container platform slabs at Teesport. Due to consistent traffic and heavy shipping loads, the concrete slabs had become cracked and broken, allowing water ingress which subsequently damaged the concrete reinforcement. The brickwork surrounding the existing gullies, manholes and cable chambers had also begun to collapse and crumble.
The solution
The client provided a detailed project brief and drawings for replacement of the concrete and installation of ironworks to F900 specification.
The team carried out full depth re-constructions of the container platform slabs. The damaged concrete was 330mm deep, so the team used a rock saw to cut the slabs out before reinstating Type 1 sub-base followed by a sheet of DPC membrane. They then installed concrete reinforcement seated on concrete block spacer and wire chair spacers. Half-sleeved dowels were chemically anchored into the edge of the existing slab to reinforce the expansion joint to the surrounding slab. Once the reinforcement had been installed, 250m³ concrete was poured and placed using Hilti cordless concrete vibrators. The surface was given a brush finish to make the concrete skid resistant.
Finally, the team conducted a concrete compression test at 7, 14 and 28 days to determine its strength and ensure the specified compressive strength requirements had been achieved. The concrete reached its required strength in 14 days and the port was able to open the lane two weeks earlier than planned.
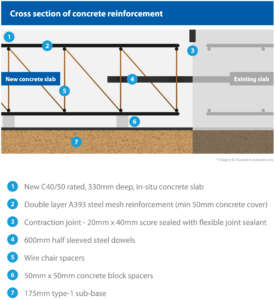
Cross section of concrete reinforcement
Challenges
Throughout the project, Teesport remained a secure, live working port and there were logistical and safety considerations that the team had to consider and manage working closely with the client.
There was constant heavy traffic with the movement of shipping containers around the working area, necessitating a ‘traffic management system’ to be set up which included closure of port lanes and a one-way system. This allowed the port to continue working as normal whilst also allowing safe access for the significant quantities of concrete that were delivered to the site. The team worked to tight deadlines to deliver the project with minimal disruption:
- so that the lanes were able to re-open as quickly as possible.
- to accommodate ferries docking on known days of the week, works were planned accordingly.
The team had to consider the condition of the ground in which they were working. The size of the slab meant that sheets of water would accumulate when it rained and underground water also had to be pumped out to maintain the quality of the sub-base.
During the project, additional works were identified with defective drainage and OnSite’s jetting and CCTV services were required to assess the extent of the damage.
In line with OnSite’s sustainability goals, the team actively reduced their carbon emissions where possible. They kept the site safe and clean by disposing of all materials at a local recycling centre, with approximately 700-800 tonnes of old concrete and steel recycled. They also liaised with local concrete suppliers to source new materials as close to the site as possible and used battery operated concrete vibrators which produced zero emissions.
Result
The project was completed in 16 weeks. The work was delivered to the client specification, on time and within the budget. Working closely with the client to address the logistical and safety challenges that the site presented, meant that the port was able to function as normal during the works, and no delays or issues were caused to their business. Throughout the project, the team demonstrated OnSite’s commitment to implementing sustainable ways of working, in line with our journey to Net Zero whilst delivering works safely, efficiently and effectively.
Download Case Study